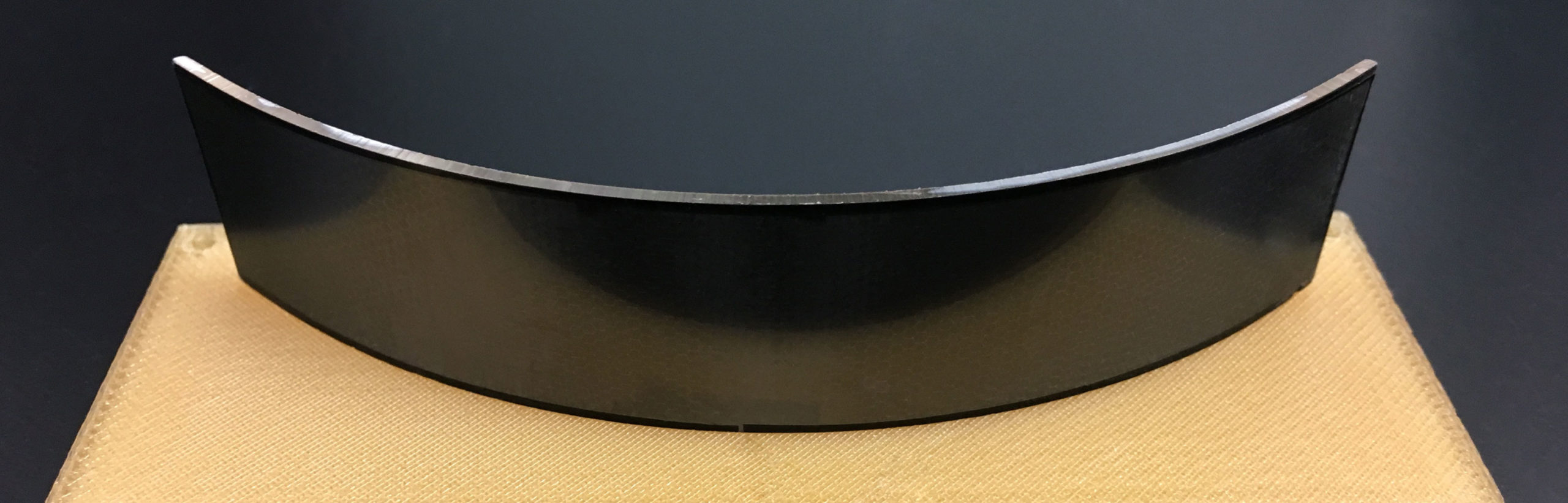
Enabling the vision of tomorrow through photon and electron amplification.
Incom’s MCP technology utilizes a proprietary fabrication method co-developed with Argonne National Laboratory enabling the largest imaging area available and fully customizable geometries. It combines Incom’s capillary arrays (GCA) with thin film coatings applied to the channels by atomic layer deposition (ALD), which functionalizes the MCPs and allows the final operational parameters to be tailored to specific applications. Incom’s ALD-GCA-MCP technology offers significant advantages over conventional lead-oxide based MCP technology.
Features
Applications
Curved MCP
Used in Space Flight Mass Spectrometry
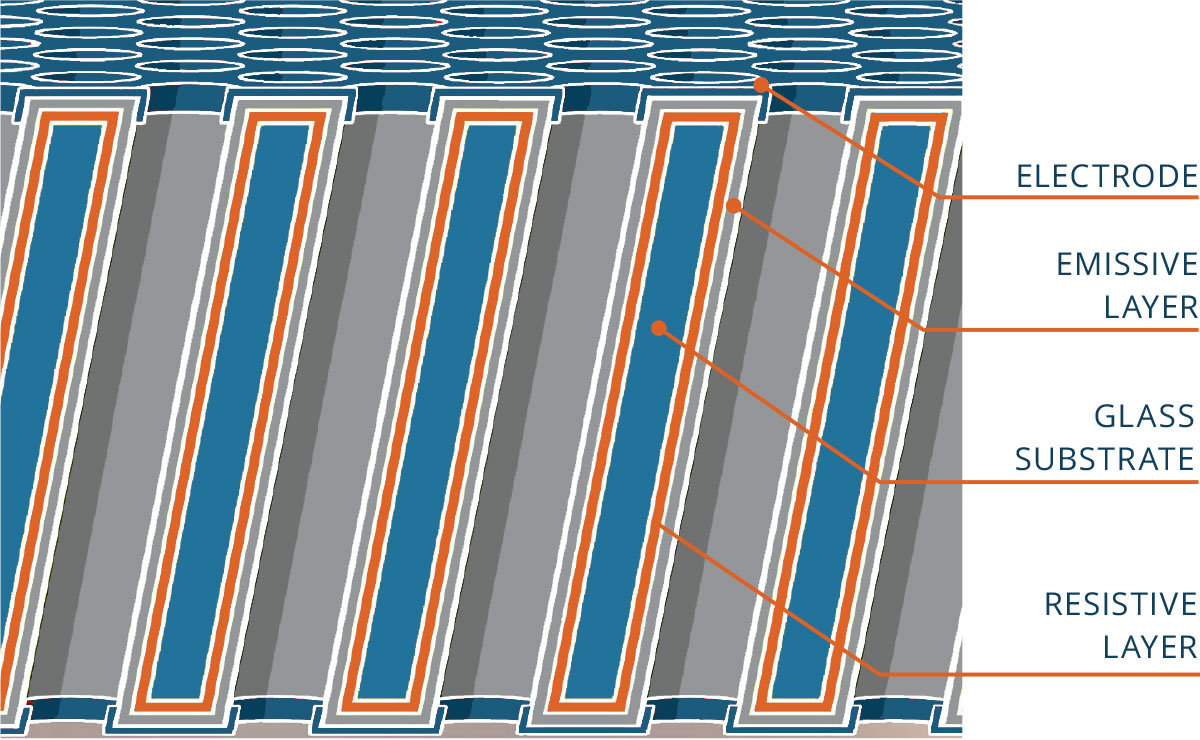
Glass capillary arrays functionalized with atomic layer deposition resistive and emissive coatings.
MCP gain at 1000 V | >1 x 104 |
Open area ratio | ≥ 65% |
SEE Materials | Al2O3 or MgO |
Resistance range | Fully customizable |
Background | <0.05 events / sec / cm2 |
Gain stability | > 7 C/cm2 |
Gama ray sensitivity | ~ 3X lower than conventional PbO-MCPs |
L/d | 60:1 (customizable upon request) |
Bias angle | 13° (customizable upon request) |
Pore size | 5μm, 10μm, 20μm |
Part dimensions | Up to 20 cm x 20 cm |